01
Werkzeuge und Ausstattung
Die Entwicklung und Produktion von Prototypen benötigt die passenden Werkzeuge, Kenntnisse und Erfahrungen. Unsere Ingenieurexpertise und 3D-Modellierungssoftware reduzieren die Zeit für Design und Fertigung von Prototypenteilen deutlich, ähnlich wie die Werkzeuge in FDM- und SLS-Prozessen.
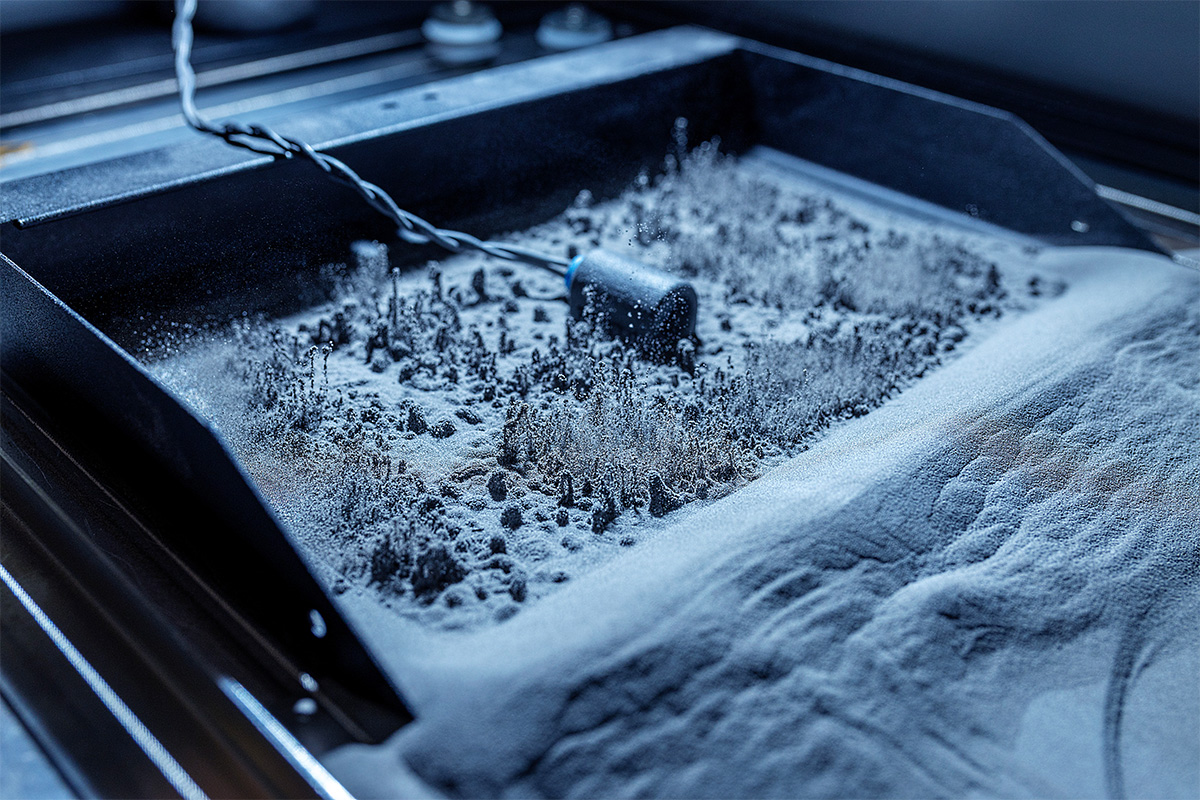
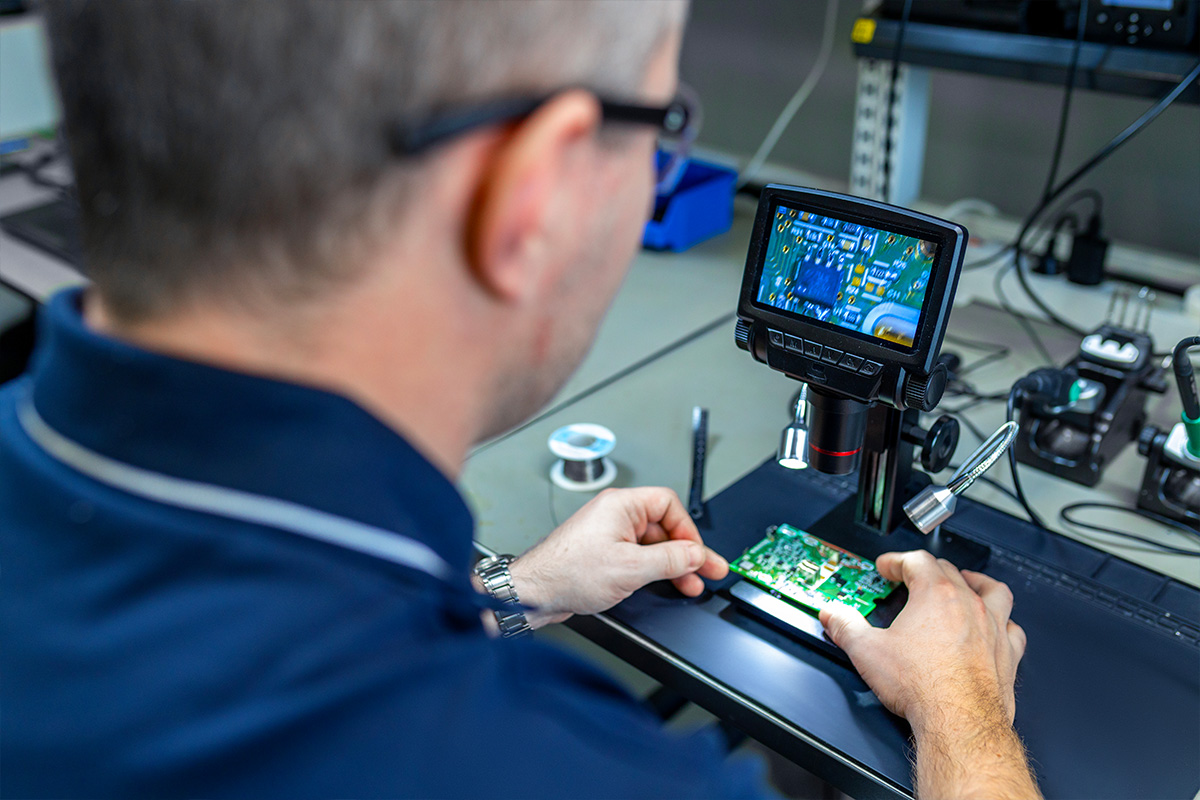
02
Tests
und Programmierung
Hochwertige Produkte erfordern umfassende Tests in allen Phasen des Produktionsprozesses. Wir führen diese nach höchsten Standards entweder direkt an der Produktionslinie oder in unseren Labors durch. Mit der Software LabVIEW entwerfen und programmieren wir Testsequenzen und nutzen das technische Know-how sowie die Kompetenzen unseres internen Test- und Validierungsteams. Indem wir Geräte autonom betreiben und flexibel auf sich ändernde Kundenanforderungen reagieren, sichern wir Ihnen einen Wettbewerbsvorteil über den gesamten Produktlebenszyklus.
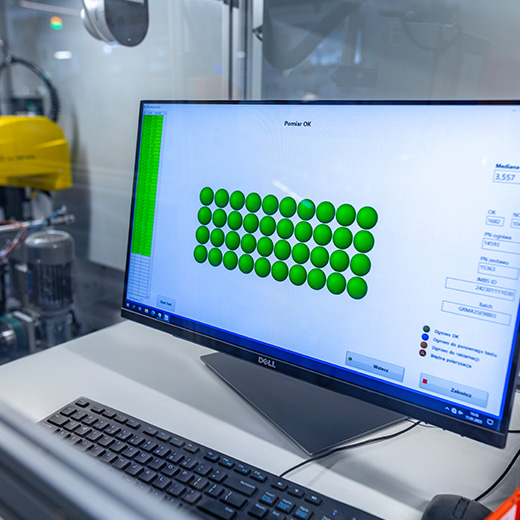
Tests – Pre-Test
Ein Pre-Test ist eine der ersten Testphasen, in der einzelne Zellen mittels drei Algorithmen (Min-Max, Median, Durchschnittswert) geprüft werden. Dies sichert die optimale Übereinstimmung aller einzelnen Zellen, die eine Batterie bilden.
Parameter
3 Arten von Algorithmen (Min-Max, Median, Durchschnittswert) |
Tatsächliche Ansicht der Zelle |
Akustische Störungsanzeige |
Polarisationsfehler und Batteriespannungsfehler werden getrennt angezeigt |
Möglichkeit der Visualisierung einer beliebigen Batterieform |
Datenprotokollierung in CSV-Dateien, mögliche Verbindung zu einer Datenbank |
Standardauflösung alle 1 mV |
Auslösung auf Knopfdruck oder automatisch |
Kommunikation über Ethernet |
Messung des Innenwiderstands einer ACIR-Zelle |
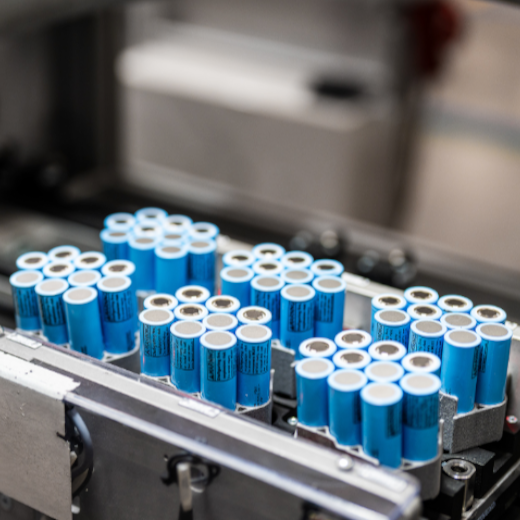
Tests – Zwischentest
Ein Zwischentest ist der Test von Zellmodulen in einem Zwischenstadium des Prozesses. Wir führen diese Art von Test durch, um zu gewährleisten, dass die Blöcke, aus denen die Batterie besteht, korrekt aufeinander abgestimmt sind.
Parameter
Tatsächliche Ansicht der Zelle |
Akustische Störungsanzeige |
Polarisationsfehler und Batteriespannungsfehler werden getrennt angezeigt |
Möglichkeit der Visualisierung einer beliebigen Batterieform |
Datenprotokollierung in CSV-Dateien, mögliche Verbindung zu einer Datenbank |
Standardauflösung alle 1 mV |
Kommunikation über Ethernet |
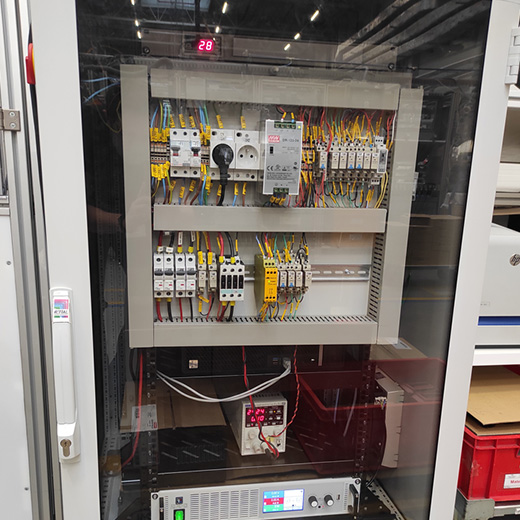
Tests – EOL test
Der EOL-Test, durchgeführt in der letzten Phase der Batteriemontage, überprüft die Parameter mit einem Adapter. Dieser dient dazu, die Anschlussbuchse des Benutzers zu testen und die korrekte Funktion der Batterie zu bestätigen.
Parameter
Kommunikation – CAN, UART |
Lasttests bis zu 200 A |
Ladetests bis zu 60 A |
Kurzschluss-Tests |
LED-Monitoring |
Button Test |
Drucken von Etiketten und Überprüfung durch Scannen des QR-Codes |
Datenaufzeichnung in CSV-Datei |
Dedizierter Adapter – kann gegen ein anderes Batteriemodell ausgetauscht werden |

PCB-Programmierung
Wir nutzen einen speziellen Adapter, um die Programmierung der Leiterplatte sicherzustellen. Dieser Programmieradapter dient auch zur Überprüfung der montierten Tasten auf der Leiterplatte, um deren korrekten Betrieb vor dem Einbau in die Batterie zu gewährleisten.
Wichtigste Geräteparameter
Tastenpositionskontrolle mit einer Genauigkeit von 10 µm |
PCB-Test und Leiterplatten-Programmierung |
Datenaufzeichnung in CSV-Datei |
Automatische temperaturabhängige Anpassung |
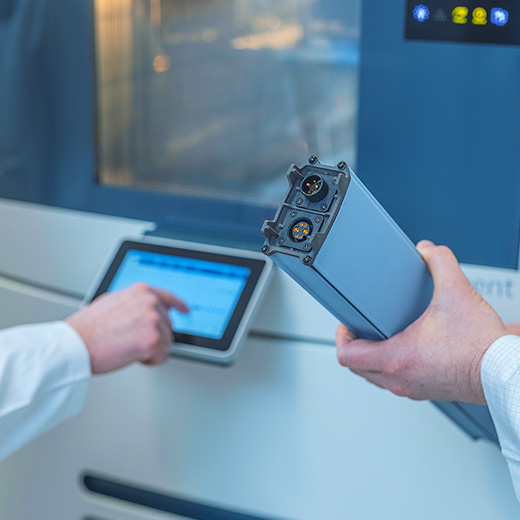
Tests – Ursachen-Analyse von Batterieproblemen
Das Testen ist ein grundlegender Prozess, der es uns ermöglicht, die ordnungsgemäße Funktion der Batterie zu gewährleisten und mögliche Fehler zu beseitigen. Wenn Probleme mit der Batterie auftreten, unterstützen wir Sie bei der Identifizierung und Behebung von Problemen, indem wir folgende Tests durchführen:
- elektrische Tests zur Überprüfung aller fraglichen Komponenten,
- mikroskopische Analysen,
- Laboruntersuchungen.
03
ESD – Schutz vor elektrostatischer Entladung
Der ESD-Schutz (Electro-Static Discharge) ist ein System, das die Sicherheit elektronischer Komponenten gewährleistet, die empfindlich auf elektrostatische Entladungen reagieren. Ladungsfluss und Hochspannung können Komponenten in jeder Phase der Produktion, des Transports oder der Verwendung beschädigen. Ein ordnungsgemäßer ESD-Schutz von Produkten ist eine Garantie für deren hohe Qualität und einwandfreie Funktion.
EPA-Zone – Ein Produktionsbereich, der in Bezug auf das Vorhandensein von Gegenständen und ESD-Aktivität sicher ist, wird als EPA-Zone (Electro-Static Protection Area) bezeichnet. Diese Zone ist mit Sperrstreifen und Informationsetiketten gekennzeichnet. Die EPA-Zone wird auf ihre Einhaltung geprüft und mit einem Zertifikat bestätigt.
ESD-Koordinator – Wir haben eine kompetente und erfahrene Person in unserem Team, die für die Belange des ESD-Schutzes verantwortlich ist. Zu den Aufgaben dieser Person gehört das Führen einer Liste aller für den ESD-Schutz zugelassenen Geräte und Gegenstände sowie die Durchführung regelmäßiger Messungen und Verfahren für ein sicheres Mitarbeiterverhalten. Der ESD-Koordinator fungiert als Prüfer bei Inspektionsaudits und gewährleistet außerdem, dass die ESD-Bedingungen erfüllt werden, die durch die von der Internationalen Europäischen Kommission entwickelten Normen EN 61340-5-1:2009 und EN 61340-5-2:2002 definiert sind.
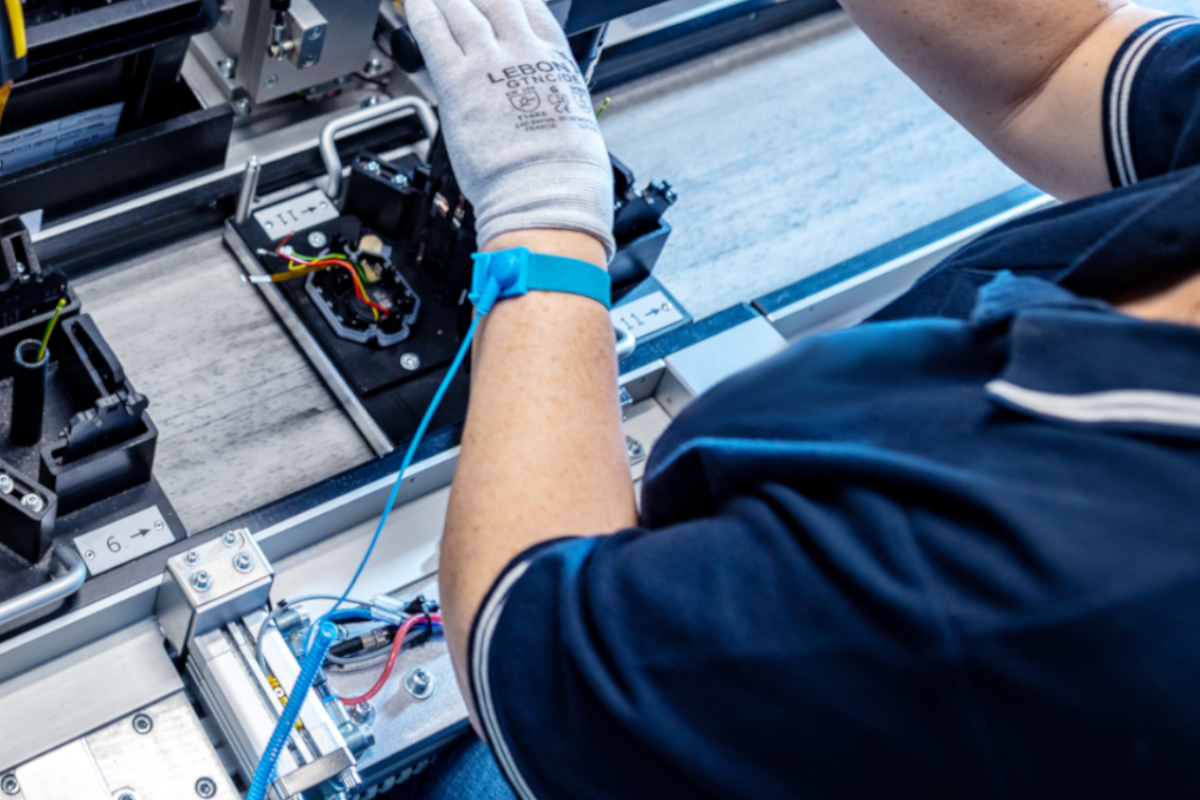
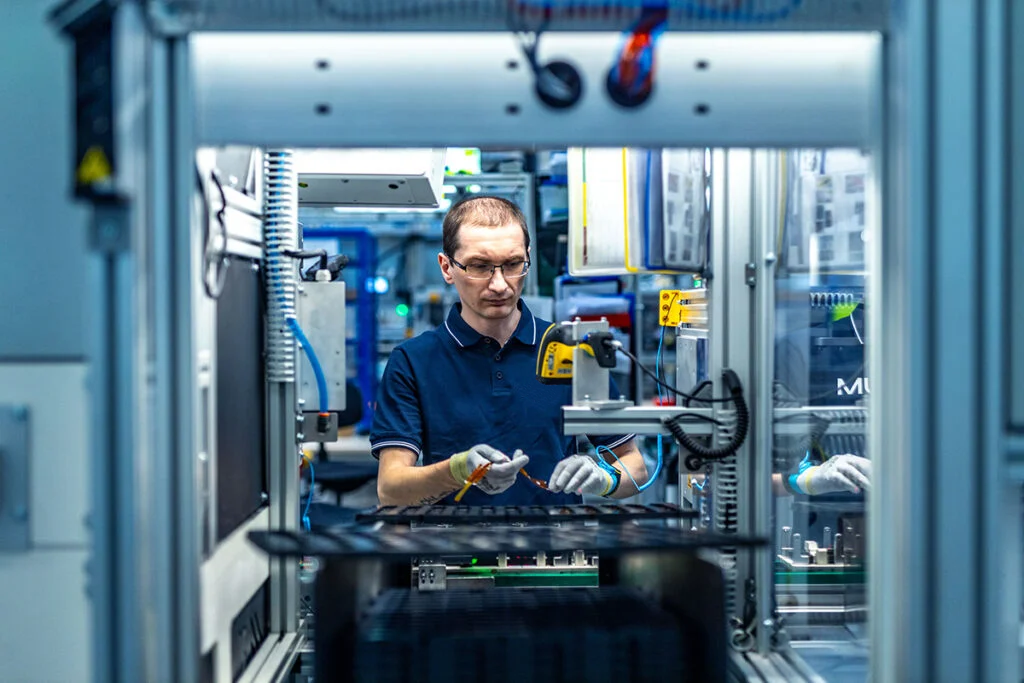
ESD-Schutz für Mitarbeiter
Wir schulen unsere Mitarbeiter regelmäßig in Sachen ESD-Sicherheit. Das wichtigste Element zum Schutz der Mitarbeiter ist die Erdung des Arbeitsplatzes. Die Sicherheit am Arbeitsplatz wird durch speziell angepasste Arbeitsplätze mit doppellagigen Tischmatten und Armbändern gewährleistet, die Ladungen vom Körper ableiten. Die im EPA-Bereich anwesenden Teammitglieder tragen ESD-Arbeitskleidung, Handschuhe und spezielles Schuhwerk oder Protektoren mit einem leitfähigen Schuhband.
04
Schweißen
Das Schweißen beeinflusst die Qualität von Batterien erheblich, indem es ihre elektrischen Eigenschaften in verschiedenen Phasen bestimmt. Der Prozess beginnt mit der Auswahl der Materialien und der Festlegung der Verbindungsarten und Schweißtechniken.
Die gewählten Schweißverfahren, insbesondere das Widerstandsschweißen, müssen Tests und Validierungen unterzogen werden, um zu gewährleisten, dass sie die Kundenanforderungen erfüllen und stabil und widerstandsfähig sind.
In der Batterieproduktion werden zahlreiche Verbindungen mit Hilfe des Widerstandsschweißens hergestellt, wobei die Parameter jeder Verbindung individuell gemäß den Normen und Verfahren entwickelt werden.
Zu den Schlüsselfaktoren beim Widerstandsschweißen gehören die Auswahl der richtigen Geräte und Elektroden sowie die Festlegung und Überwachung der Prozessparameter (wie Spannung, Strom und Zeit) in Echtzeit, um die Prozessintegrität zu gewährleisten.
Schließlich wird die Qualität der geschweißten Verbindungen sowohl mit zerstörenden (z.B. Bruch- und Härtetests) als auch mit zerstörungsfreien Methoden (z.B. Metallographie, Röntgen) bewertet, um die Zuverlässigkeit und Qualität der Schweißung zu gewährleisten.
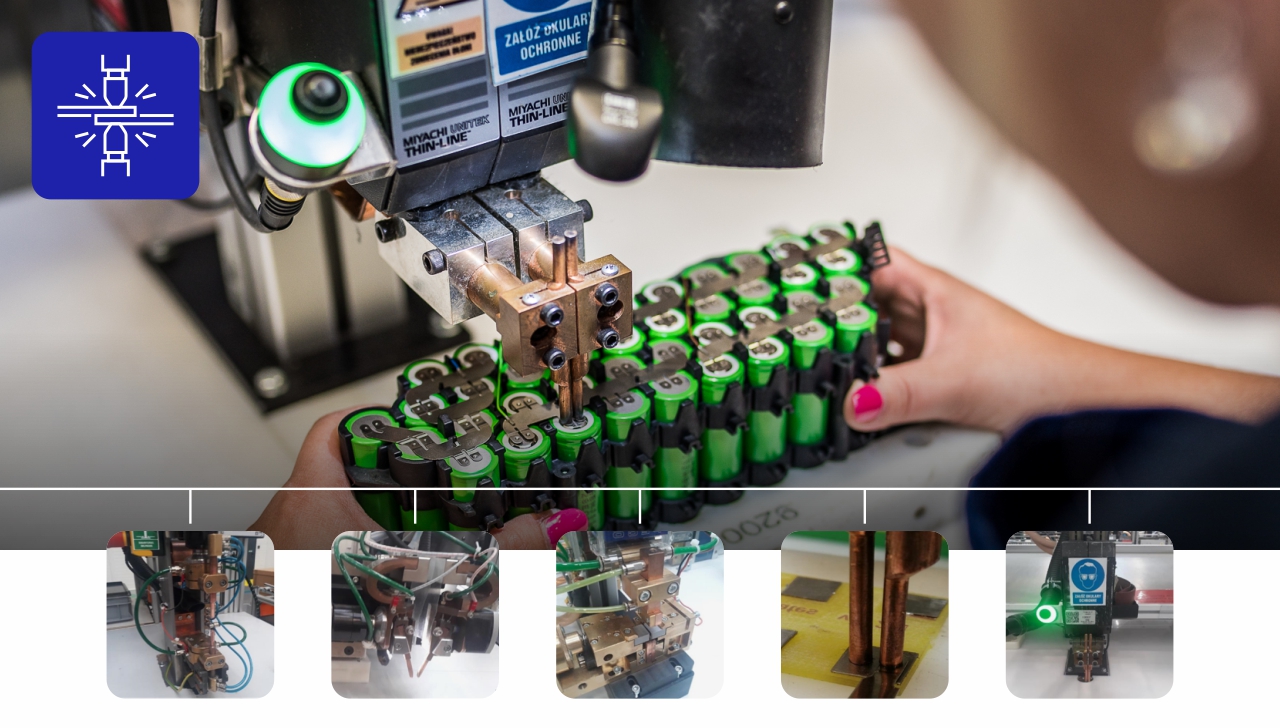
Schweißarten
Widerstandsschweißen
- Punktschweißen,
- Kompaktschweißen,
- Spaltschweißen,
- Schrittschweißen,
- Zangenschweißen.
Schweißen – Validierung und Eignungsprüfung
Ein wichtiger Schritt im Schweißprozess ist die Validierung und Eignungsprüfung. Wir führen diese Tests wie folgt durch:
- Analyse der Schweißspezifikationen.
- Schweißtests (definiertes Material und Elektrodenform).
- die Einstellung der Schweißprozessparameter (auch MIN- und MAX-Werte).
- Validierung/SPC.
- X-RAY-Analyse und/oder Metallographie.
- Dokumentation der Schweißprozessparameter.
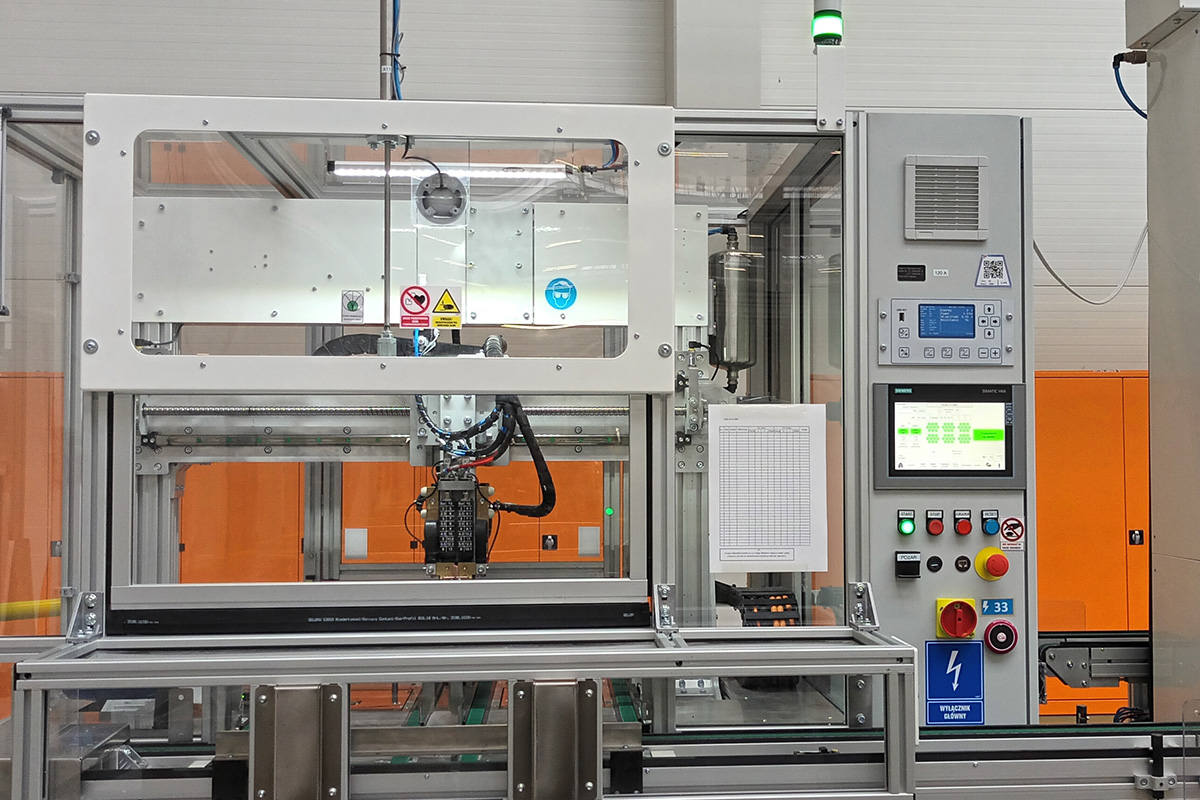
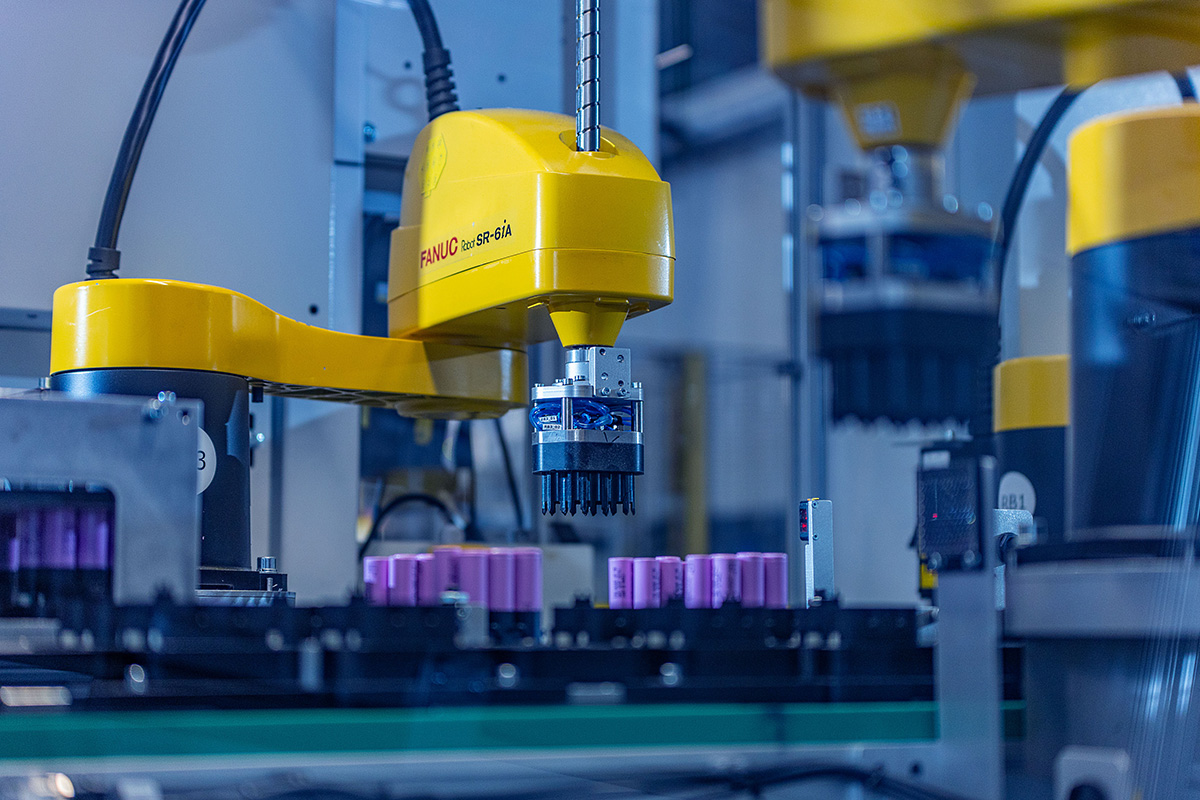
05
Automatisierung – Zellentest und Monatge
Die Automatisierung des Zelltest- und Montageprozesses besteht aus folgenden Schritten:
- Messung der Spannung und der Polarität jeder Zelle.
- Vergleich der Spannung zwischen den Zellen.
- Platzierung der Zellen in den Zellenhaltern durch Roboter.
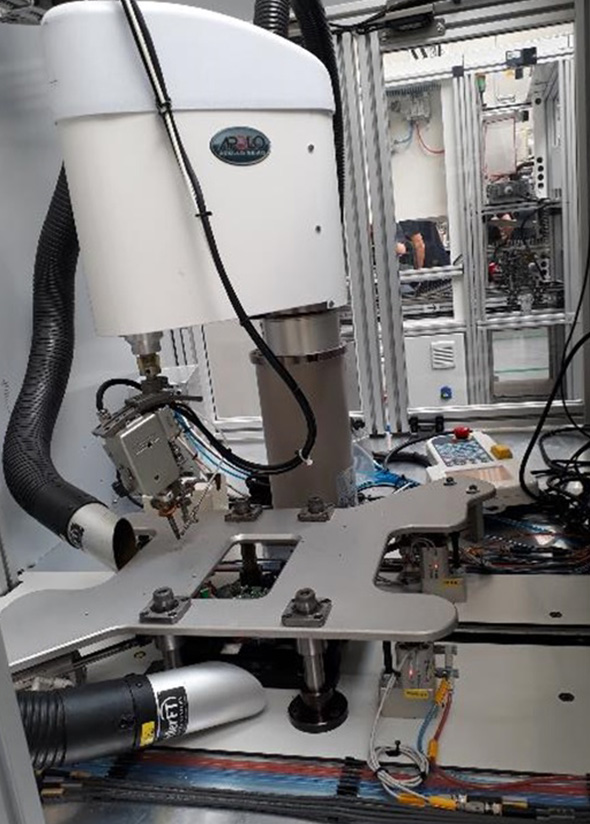
Automatisierung – der Lötprozess
Das Löten ist ein weit verbreiteter Prozess in der Batterieproduktion, der vollautomatisch durchgeführt werden kann. Der Prozess des automatisierten Lötens basiert auf einem System mit SCARA-Robotern, einem Lötkopf, einem Zinnspendesystem und einem Temperaturregler. Der Einsatz dieser Lösung erhöht die Sicherheit, die Produktivität, die Präzision sowie die Wiederholbarkeit und die Qualität der Lötstellen erheblich. Das von SCARA-Robotern verwendete System ermöglicht:
- Durchführung eines wiederholbaren Prozesses, der die korrekte Lötstelle gewährleistet.
- Kontrolle der Prozessparameter.
- Verringerung des Risikos von “kaltem Lötzinn”.
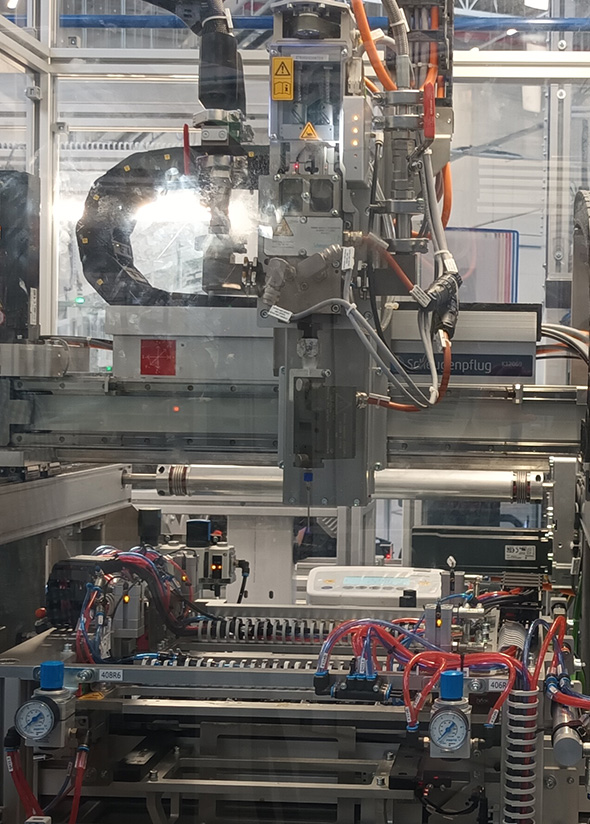
Automatisierung – Verschraubungs-/Verdrillungsprozess
Die Automatisierung des Verdrillprozesses in der Batterieproduktion ermöglicht eine höhere Produktivität, die Kontrolle des Ablaufs, die Festlegung der Verdrillstrategie und die Überwachung und Aufzeichnung der Parameter des Verdrillprozesses (z.B. Drehmoment, Winkel, Ablauf).
Das automatische Verdrillsystem umfasst:
- einen fortschrittlichen Treiber/Controller.
- Schraubenschlüssel mit Dehnungsmessstreifen oder Stromsensor.
- Teilezuführung.
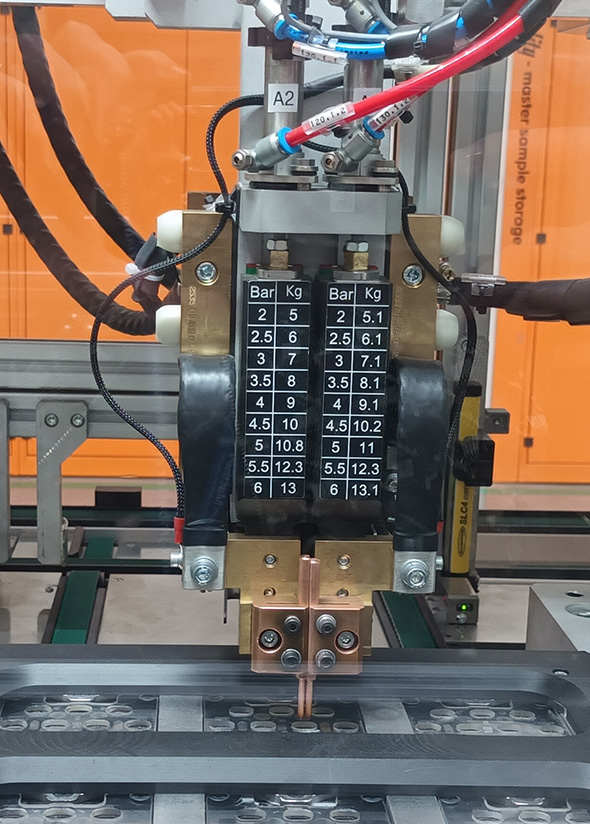
Automatisierung – Schweißen
Beim automatisierten Schweißprozess geht es hauptsächlich um:
- präzise Produktpositionierung.
- automatische Kontrolle der Schweißparameter und NOK-Erkennung.
- hohe Effizienz des Schweißprozesses.
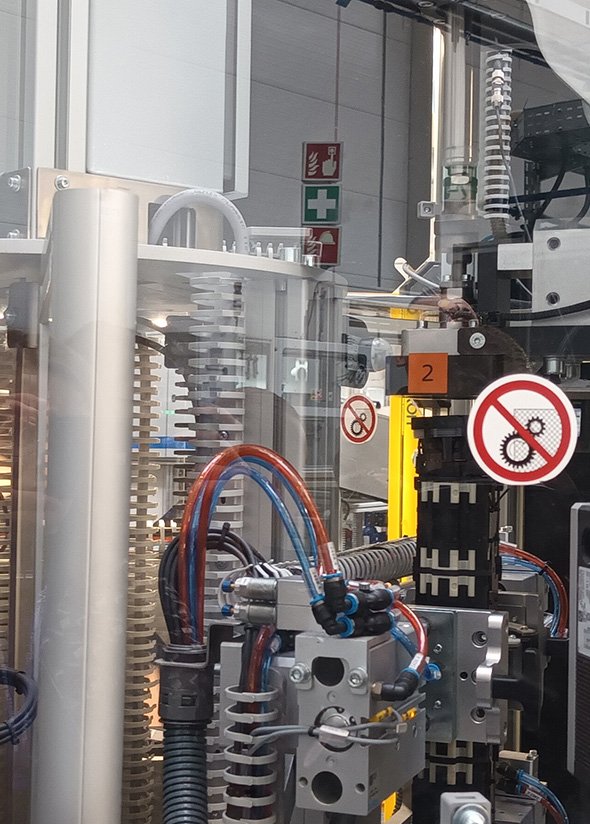
Pressen
Der automatisierte Pressvorgang ist:
- Kontrolle der Prozessparameter (Anpresskraft und Verschiebung).
- NOK-Erkennung.
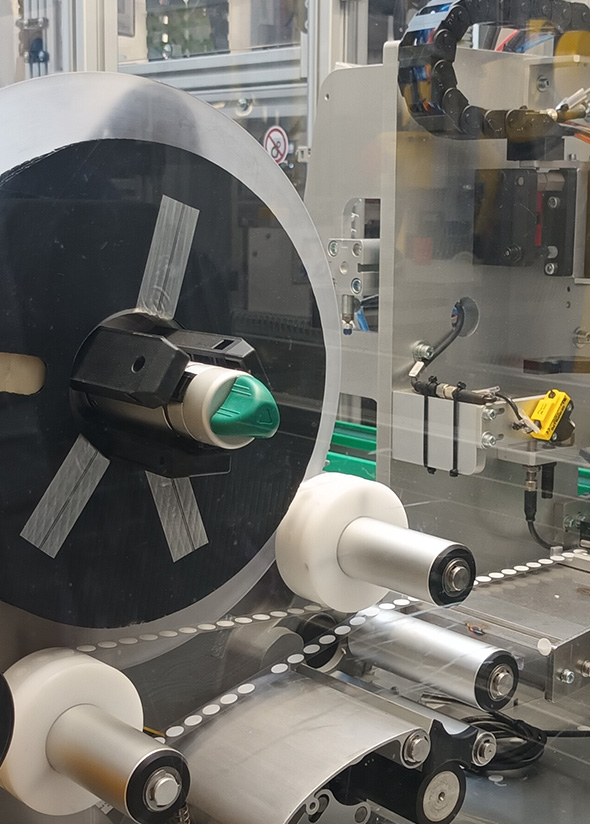
Membrane application
Membrane application consists of the following steps:
- automated membrane application,
- integrated air flow measurement,
- NOK detection.
Applikation der Membrane
Das Aufbringen der Membrane besteht aus den folgenden Schritten:
- automatisierte Membranapplikation.
- integrierte Luftstrommessung.
- NOK-Erkennung.
06
Dosierung und Verguss
Der Zweck des Dosierens oder Vergießens ist es, die Sicherheit und Lebensdauer kritischer Komponenten (z.B. Elektronik) zu erhöhen und eine ordnungsgemäße Abdichtung zu gewährleisten.
2-Komponenten-Verguss und Dosierung
Der 2-Komponenten-Verguss und das Auftragen (einschließlich des Auftragens von Wärmeleitpaste) werden mit einer automatischen Station durchgeführt, die ein fortschrittliches Komponenten-Zuführ- und Mischsystem sowie einen auf einem kartesischen Roboter montierten Kopf umfasst. Dadurch sind die oben erwähnten Prozesse sehr präzise und wiederholbar.
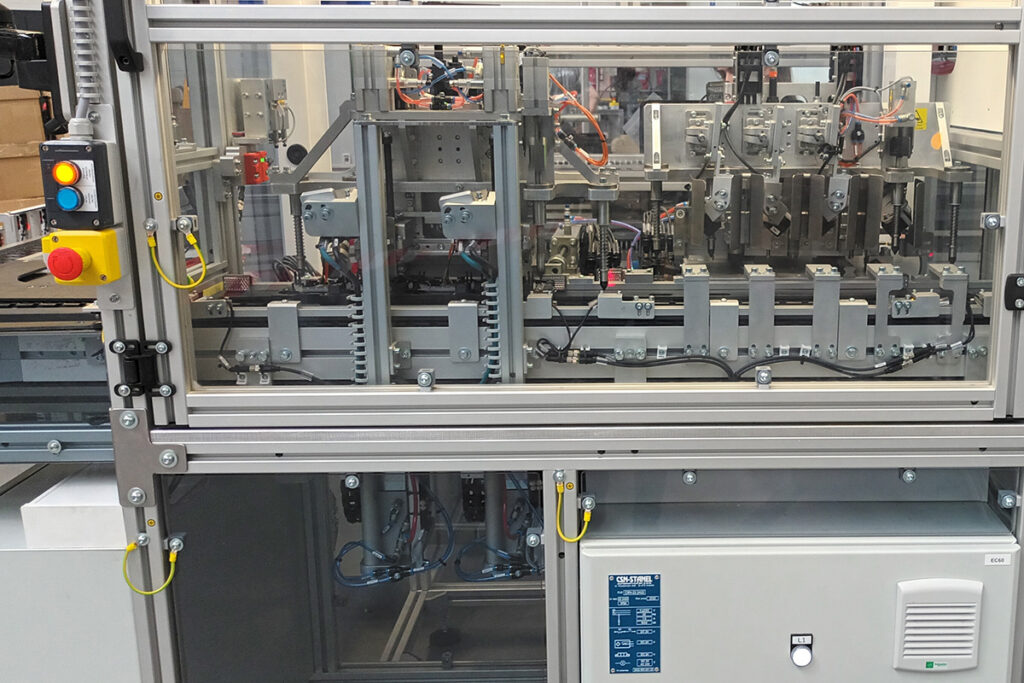
07
Produktkennzeichnung
Der letzte Schritt im Produktionsprozess ist die Produktkennzeichnung. Wir führen den gesamten Kennzeichnungsprozess in Übereinstimmung mit den geltenden Normen und gesetzlichen Bestimmungen durch.
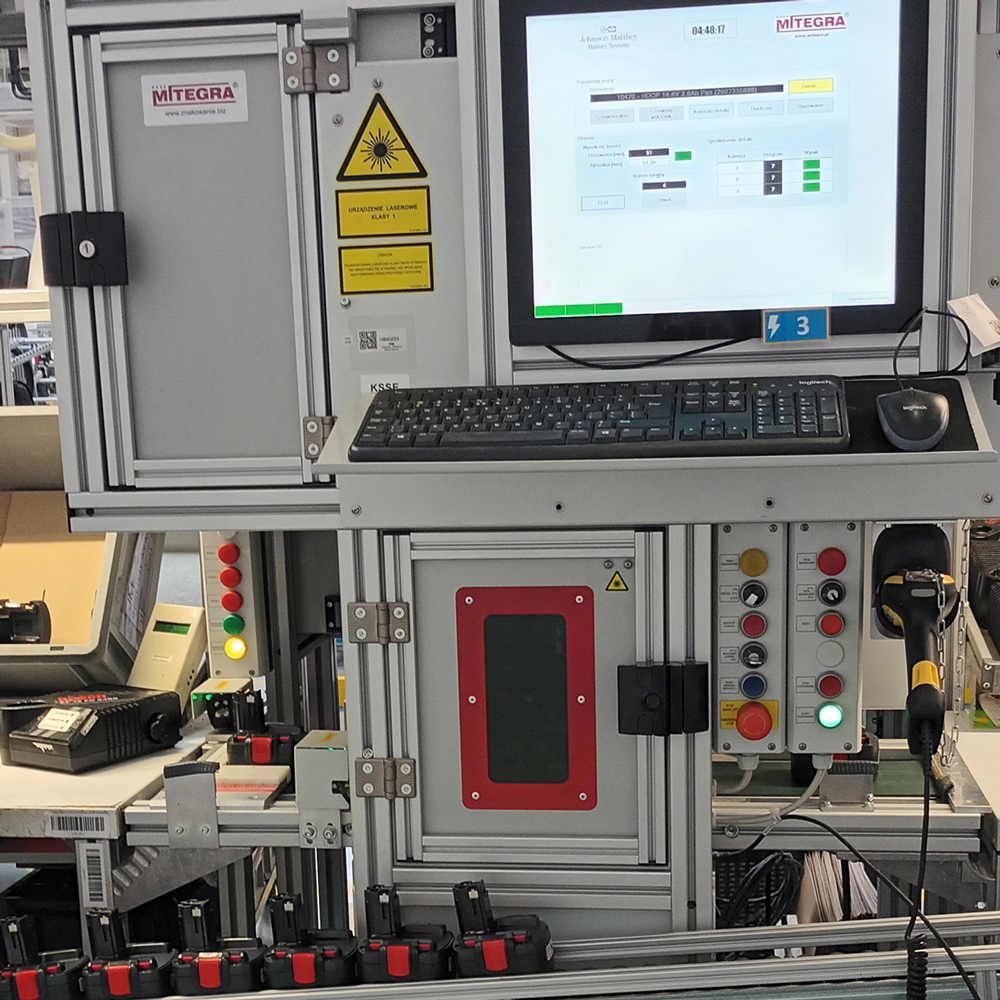
Wir kennzeichnen Produkte mit den folgenden Techniken:
- Lasermarkierung.
- Tampondruck.
- Aufklebeetiketten, die mit der Thermotransfertechnik gedruckt werden.
Die Laserkennzeichnung ist ein automatisiertes Verfahren, das eine sehr schnelle, reproduzierbare Kennzeichnung von Daten ermöglicht, die von anderen Geräten übertragen werden, z.B. die vom EoL-Tester vergebene Seriennummer.
Der Tampondruck ist eine Technik, mit der unter anderem die Beschreibung und das Logo des Herstellers auf das Produkt aufgebracht werden. Der große Vorteil des Tampondrucks ist, dass er auf jede Oberfläche gedruckt werden kann. Ein glatter Silikontampon (Drucktampon) mit hoher chemischer Beständigkeit wird verwendet, um die Farbe von der Druckplatte auf das Objekt zu übertragen.
08
Datenerfassung
und Teileidentifikation
Unser Rückverfolgbarkeits-System ermöglicht die Rückverfolgung aller Komponenten, der im Prozess verwendeten technologischen Parameter und die Zuweisung von Kontrolldaten, sofern definiert. Die Rückverfolgbarkeit der Teile in der Produktion wird durch die Lieferung der Teile in etikettierten Behältern unter Verwendung von Barcodes, QR oder DMC erreicht.
Ein wesentlicher Bestandteil des Produktionsprozesses ist die Identifizierung der Teile in jeder Phase und die Zuweisung der relevanten Daten zu den Teilen. Dies wird durch die eingesetzte RFID-Technologie ermöglicht. Die zugeordneten Daten ermöglichen uns eine genaue Analyse und Optimierung der Prozesse und Zeiten.
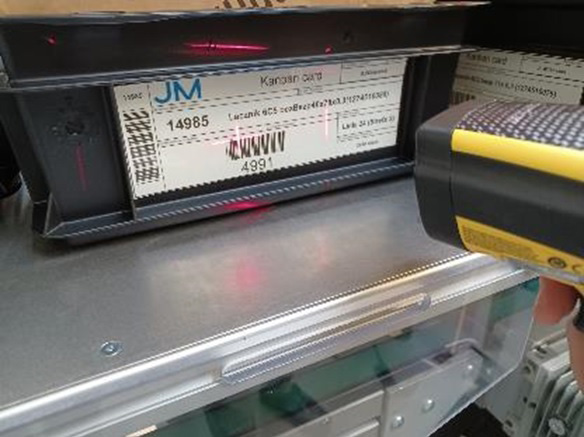
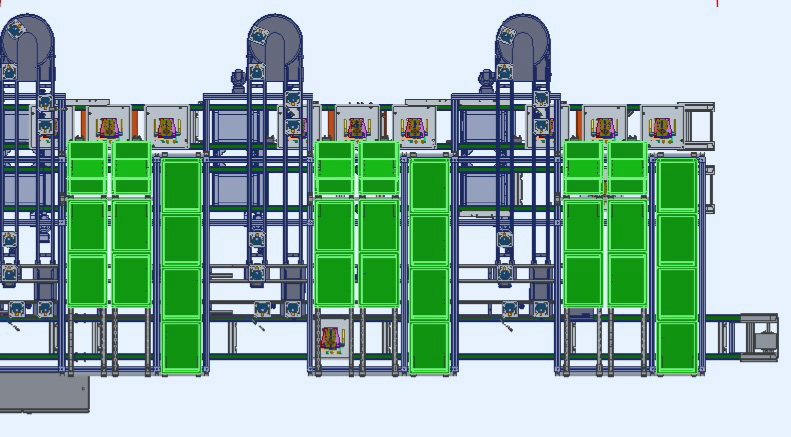
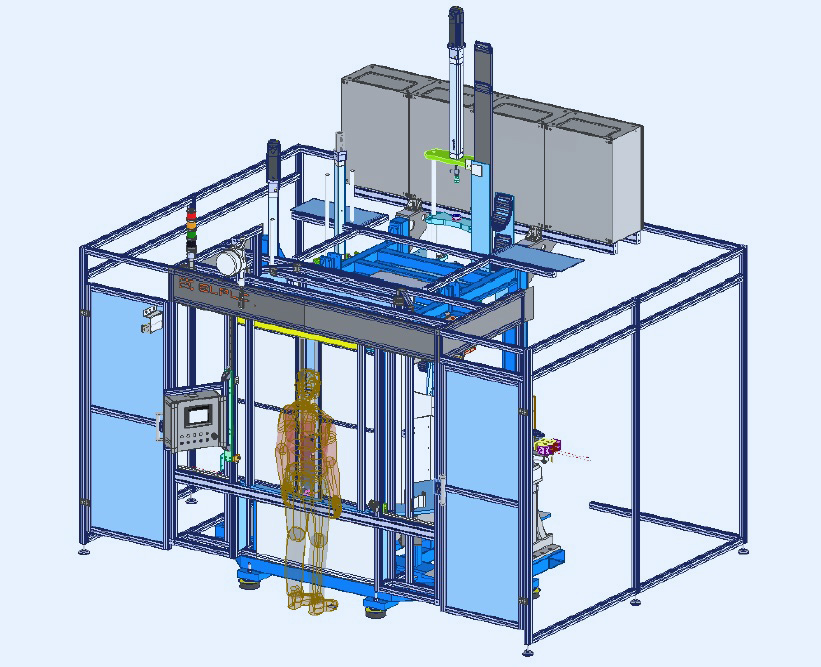
09
Inbetriebnahme der Maschine/Produktionslinie
Die Inbetriebnahme einer Maschine/Produktionslinie erfordert eine angemessene Vorbereitung. Der gesamte Prozess wird in Übereinstimmung mit den entwickelten Verfahren und den gesetzlichen und sicherheitstechnischen Anforderungen durchgeführt. Der Startvorgang umfasst einzelne Phasen, die aus folgenden Punkten bestehen:
Erstellung von Maschinenspezifikationen
- erfolgt auf der Grundlage eines entwickelten Prozesses.
- deckt alle Kundenanforderungen ab.
- deckt alle allgemeinen EMBS-Anforderungen und Automatisierungsstandards ab.
Abnahme des 3D-Modells
- In dieser Phase werden die meisten Konstruktionsfehler und konzeptionellen Schwächen entdeckt.
Abholung der Maschine/Linie beim Lieferanten
- Verifizierung der Sicherheitssysteme.
- Erste Tests und Probeproduktion.
- Überprüfung der Übereinstimmung mit den Anforderungen.
Endabnahme
- Verifizierung bei Run@Rate.